Exploring the Benefits of 3D Scanning: Transforming Industries and Innovation
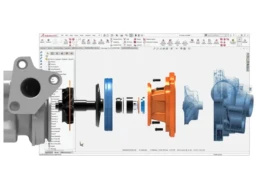
Handheld 3D scanners are revolutionising industries ranging from automotive to aerospace and power generation. By providing unmatched precision, speed, and convenience, these cutting-edge tools are transforming how engineers and specialists perform quality control (QC) and reverse engineering.
Whether you’re a manufacturing engineer, quality control specialist, product designer, or metrology expert, understanding the potential of this technology is key to staying competitive in a data-driven world. This guide dives deeply into how handheld 3D scanners enhance accuracy, efficiency, and cost-effectiveness. Plus, we’ll discuss real-world use cases, key features to consider, and how to select the right scanner for your needs.
Why Handheld 3D Scanners Are the Future of Quality Control
Precision Measurement Made Simple
One of the most appealing aspects of handheld 3D scanners is their capability to deliver incredibly high accuracy, often down to micrometers. Advanced technologies, such as the SIMSCAN-E, NIMBLETRACK, and TRACKSCAN SHARP-S employ blue light laser technology to create highly detailed 3D representations of objects.
This level of precision is invaluable for maintaining tight tolerances in industries like aerospace and automotive, where even the smallest deviation can have significant consequences. Unlike traditional inspection tools, handheld 3D scanners can perform non-contact measurements, reducing risks of damage or disruptions to the surface.
Not only does this make inspections faster, but it also eliminates the need for extensive fixturing and environmental controls—a common pain point in conventional QC methods.
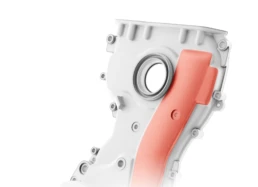
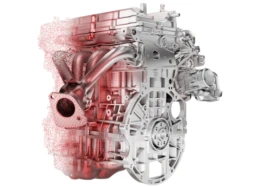
Enhanced Efficiency in Inspection
Time is money, and handheld 3D scanners excel at saving both. Features such as rapid data capture mean these devices can gather hundreds of thousands of data points in just seconds, drastically reducing inspection times. A process that once took hours can now be completed in mere minutes.
Take the automotive sector as an example. Components are often scanned directly on the production line to ensure they meet exact specifications, preventing costly recalls or production delays. Additionally, their portability allows engineers to conduct inspections in any environment—whether on-site, in confined spaces, or in a dedicated production lab.
Cost-Effectiveness Over Time
By enabling fast issue detection early in the manufacturing or prototyping stages, handheld 3D scanners minimise rework, defects, and downtime. Traditional measurement equipment often requires multiple setups or specialised infrastructure, inflating costs. Portable 3D laser scanners, on the other hand, streamline workflows while offering an excellent return on investment (ROI).
Applications of Handheld 3D Scanners in Industry
Quality Control Across Multi-Sector Workflows
Whether it’s aerospace parts, automotive gear assemblies, or heavy-duty power-generation turbines, handheld 3D scanners cater to various quality control needs. By capturing fine surface details and detecting microscopic imperfections, these scanners ensure components meet regulatory and safety standards.