The Importance of Automated 3D Scanning for Quality Control and Inspection
In the ever-evolving landscape of manufacturing, maintaining exceptional quality control while optimising efficiency is crucial. Automated 3D scanning technology is becoming an indispensable asset in achieving these goals, providing manufacturers with advanced solutions that enhance precision, streamline operations, and support scalability.
Competitive Advantages in Quality Control
Automated 3D scanning offers unmatched precision in quality control, making it essential in industries such as aerospace, automotive, and healthcare, where even the slightest deviation can have significant consequences. High-resolution scanners capture intricate details, enabling comprehensive inspections that swiftly detect defects. By utilising colour maps and coordinate analysis, manufacturers can reduce inspection times from days to mere hours. For instance, in the aerospace industry, where the integrity of each component is vital, automated 3D scanning ensures that parts meet stringent safety and performance standards. This precision not only guarantees product reliability but also helps maintain a competitive edge by minimising recall risks and enhancing the overall product lifecycle.
Streamlining Product Development Cycles
The capabilities of automated 3D scanning extend throughout the product development cycle, from initial design to final production. In the early stages, 3D scanning facilitates the creation of accurate digital models, laying the foundation for superior product quality. As development progresses, it allows for rapid assessments and quality checks, seamlessly integrating with manual and semi-automated processes. The speed of modern scanners can revolutionise development timelines; for example, a full scan of a vehicle body, both interior and exterior, can be completed in under an hour. This efficiency enables manufacturers to iterate designs quickly, fostering innovation and reducing time-to-market for new products. In consumer electronics, for instance, this rapid iteration capability is crucial for staying ahead in a highly competitive market.
Enhancing Customer Satisfaction and Loyalty
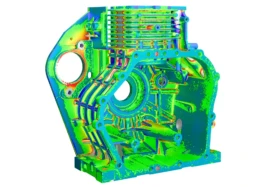
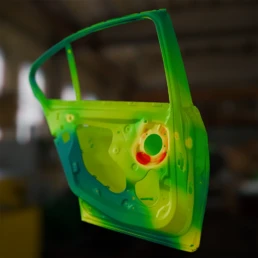
Incorporating 3D scanning into manufacturing workflows not only improves product quality but also enhances the customer experience. By delivering products that meet the highest standards of precision and quality, manufacturers can increase customer satisfaction and loyalty. The technology allows for the creation of highly detailed and visually engaging products that resonate with consumers, providing new opportunities for interaction and feedback. In sectors like the automotive industry, where customisations and personalised features are increasingly demanded, 3D scanning supports the production of bespoke components with unmatched accuracy. Furthermore, the scalability of 3D scanning systems ensures that manufacturers can adapt to changing customer needs and market trends, consistently meeting expectations and fostering long-term loyalty.
Cost-Benefit Analysis: Automated vs. Manual 3D Scanning
Transitioning to automated 3D scanning requires an initial investment, yet the long-term benefits are substantial. Automated systems significantly reduce the time and labor required for scanning tasks, allowing human resources to be allocated to more strategic areas, thus driving productivity improvements across the board. For example, repetitive scanning tasks in large-volume productions, such as those in the automotive sector, can be accomplished in minutes rather than hours. The precision and consistency offered by automated systems also minimise errors that could otherwise lead to costly rework or product recalls. Additionally, the scalability of these systems means they can grow with production demands, negating the need for continuous large-scale investments. This makes automated 3D scanning a prudent choice for manufacturers aiming to future-proof their operations.