Exploring the Benefits of 3D Scanning: Transforming Industries and Innovation
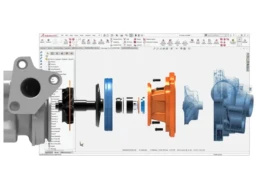
In the rapidly evolving landscape of technology, innovation is key to maintaining a competitive edge. One of the pivotal methods driving innovation is reverse engineering, particularly when combined with advanced 3D scanning techniques. This article aims to explore the fundamentals of reverse engineering, the emergence and evolution of 3D scanning, and how these two fields interact to enhance product development and innovation.
What Is Reverse Engineering?
Reverse engineering is the process of taking apart a product or system to understand its components, functionality, and design. This practice allows engineers and designers to learn from existing products, enabling them to improve upon or innovate new solutions based on collected data.
Through reverse engineering, professionals can uncover the underlying mechanics of a product without needing access to its original design documentation. By recreating an object based on its specifications, they can also identify areas of improvement and drive innovation in design and functionality.
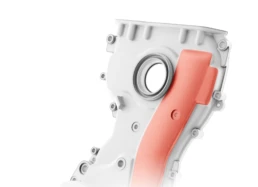
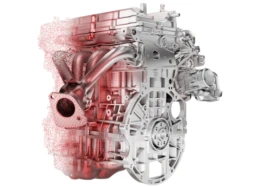
The Concept of Reverse Engineering
The basic premise of reverse engineering lies in disassembling a product to determine its construction and functionality. This can be applied not just to physical objects, but also to software and systems. Through this process, insights can be gained regarding the components used, the relationships between different parts, and potential weaknesses or inefficiencies.
This methodology is widely used in various industries, from manufacturing to software development. By understanding what makes existing products successful or less so, businesses can make informed decisions about updates, redesigns, or entirely new creations.
In the realm of software, reverse engineering can involve decompiling code to analyse its structure and functionality. This is particularly useful in cybersecurity, where understanding vulnerabilities in software can help developers patch security holes and protect users. Additionally, in the world of hardware, reverse engineering can lead to the discovery of proprietary technologies, allowing companies to create compatible products or improve their own offerings by learning from the competition.
The Role of Reverse Engineering in Innovation
Reverse engineering plays a vital role in fostering innovation. By analysing competitors’ products, businesses can identify market trends and consumer demands, allowing them to launch new features or products that align more closely with user expectations.
Moreover, it enables the enhancement of existing designs by integrating the best practices extracted from different sources. This leads to the development of more efficient designs, lower production costs, and ultimately, a stronger market presence.
Furthermore, reverse engineering can also facilitate the preservation of legacy systems. In industries where older technologies are still in use, understanding how these systems work can be crucial for maintaining and upgrading them. By documenting the inner workings of outdated products, companies can ensure that they do not lose valuable knowledge, enabling them to continue providing support and improvements long after the original manufacturer has ceased operations. This aspect of reverse engineering not only aids in innovation but also in the sustainability of technology within various sectors.
The Emergence of 3D Scanning in Reverse Engineering
As technology has advanced, so has the field of reverse engineering. One of the crucial developments in this area is the emergence of 3D scanning. This technology allows for the rapid capturing of a physical object’s shape and appearance through digital means, providing data that can be used for further analysis.The integration of 3D scanning into reverse engineering practices has opened up new avenues for precision in replication and design. Companies are now able to create highly accurate digital representations of objects, which serve as the foundation for analysis and redesign.
The Impact of 3D Scanning on Reverse Engineering
The introduction of 3D scanning technologies into reverse engineering has had a tremendous impact on how products are analysed and developed. First and foremost, the accuracy of scanned data has vastly improved the quality of models that can be created for analysis.
Additionally, the ability to obtain data quickly has shortened the duration of development cycles. This increased efficiency allows companies to respond to market changes swiftly, positioning themselves advantageously against competitors who may still rely on traditional techniques.
Moreover, the integration of 3D scanning with other technologies, such as computer-aided design (CAD) and additive manufacturing, has further enhanced the capabilities of reverse engineering. For instance, once a physical object is scanned and converted into a digital model, designers can easily manipulate the data within CAD software to innovate or improve the original design. This synergy not only streamlines the design process but also fosters creativity, enabling engineers to explore new possibilities without the constraints of physical prototypes.
Furthermore, the application of 3D scanning extends beyond just product design; it has found its way into various industries, including automotive, aerospace, and healthcare. In the automotive sector, for example, manufacturers use 3D scanning to analyse components for quality control and to ensure that replacement parts fit perfectly. In healthcare, medical professionals utilise this technology to create custom prosthetics and implants tailored to individual patients, significantly improving the outcomes of surgical procedures. The versatility of 3D scanning continues to demonstrate its value across multiple domains, solidifying its role as a transformative tool in reverse engineering.
The Process of 3D Scanning in Reverse Engineering
The process of integrating 3D scanning into reverse engineering can be broken down into several key steps. Each of these steps is crucial in ensuring that the final digital model accurately reflects the physical product.
From preparation to processing and analysis, each phase has its own requirements and implications for the reverse engineering outcome.
Steps Involved in 3D Scanning
Preparation: Ensure the object is clean and positioned correctly for scanning.
Scanning: Use a 3D scanner to capture the object’s geometry.
Post-Processing: Clean up the scanned data, removing noise and filling gaps.
Model Creation: Convert the processed point cloud into a usable 3D model.
Analysis: Evaluate the model against design requirements and identify areas for improvement.
The process is iterative, often requiring multiple scans and adjustments to obtain the most accurate representation possible.
Benefits of Using 3D Scanning in Reverse Engineering
The advantages of employing 3D scanning technologies in reverse engineering are manifold. Companies that adopt this technology can expect significant returns in efficiency, accuracy, and innovative capacity.
Enhancing Precision and Accuracy
One of the most notable benefits of 3D scanning is the enhanced precision that it affords. Unlike traditional measuring techniques, 3D scanners can capture minute details with remarkable accuracy, thus creating highly reliable digital models of the object.
This level of precision is crucial in industries such as aerospace, automotive, and healthcare, where even the slightest errors can lead to significant repercussions. By leveraging 3D scanning, companies can ensure that their product designs meet stringent quality standards.