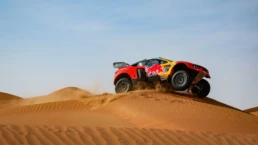
In the world of extreme sports, few events match the intensity and rigour of the Dakar Rally. It is not simply a race, but a test of endurance and resilience for both man and machine. The Dakar Rally is an annual off-road race, open to amateur and professional entries, which originated in 1978. Over the years, it has evolved into a global phenomenon, attracting participants from all corners of the earth, eager to pit their skills against some of the most challenging terrains on the planet.
The rally covers over 5,000 miles of gruelling terrain, including deserts, mountains, and savannas. This intense environment presents unique challenges to the vehicles that compete, specifically to their frames which bear the brunt of the harsh conditions.
Prodrive entered the rally in 2020 and has participated in the last three Dakar rallies, crafting a reputation for designing and manufacturing robust and high-performance race and rally cars. Their extensive experience in developing championship-winning vehicles is evident in their remarkable results. A testament to this is when Prodrive’s Hunter model secured top three positions on a Dakar stage, showcasing the company’s engineering prowess and commitment to excellence. In a recent development, Dacia announced a partnership with Prodrive to compete in the World Rally-Raid Championship (W2RC) and therefore the renowned Dakar rally from 2025. This collaboration underscores Prodrive’s established expertise in the field and its ability to forge strong partnerships with leading automakers.
“We need to monitor the health of our vehicles, particularly the space frames” - Paul Doe, Chief Chassis Engineer.
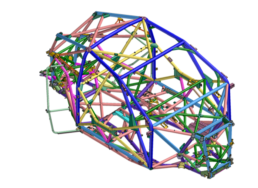
The Dakar Rally is considered one of the most challenging races globally due to its arduous terrains and extreme weather conditions. Ensuring the vehicle’s structural integrity is vital to safeguarding the driver and co-driver’s safety. Any damage or anomalies in the frame could compromise the vehicle’s stability, making it unsafe for use.
The vehicle’s frame is the backbone of its structure, affecting its overall performance. A frame that has been compromised can affect handling, speed, and reliability, all crucial factors in the demanding environment of the Dakar Rally.
Regular inspections help identify potential issues early, allowing for timely repairs and maintenance. This proactive approach extends the vehicle’s lifespan, reducing the likelihood of unexpected breakdowns or malfunctions during the race.
Post-rally inspections provide invaluable data about how the vehicle has coped with the rally’s harsh conditions. These insights are used to refine and improve the design and manufacturing processes, driving continuous improvement and innovation in 3D engineering solutions.
The inspection process of the Dakar frame is not just a routine check. It’s a comprehensive process that underpins safety, enhances performance, promotes longevity, and fuels the ongoing quest for excellence in motorsport.
The Solution: TrackScan-Sharp
“Being able to conduct large-scale measurements with Trackscan and overlay the measurement results with historical data enables us to keep an eye on what is happening with the frame” - Paul Doe, Chief Chassis Engineer.
In our endeavour to conduct a comprehensive quality and inspection analysis on Prodrive’s Dakar space frame, we leveraged the cutting-edge capabilities of the Trackscan-Sharp.
The TrackScan-Sharp is notable for its impressive 49m3 measurement volume – a first in the industry – which significantly streamlined our scanning process. This remarkable feature allowed us to obtain a complete surface scan of the Dakar shell frame without the need for frequent repositioning of the tracking system.
Trackscan-Sharp attains a measuring volume of 49m3, which allows for a tracking distance of up to 8 metres. This enabled the capture of the front and sides of the vehicle in one tracker in one position. The large area of data capture minimised the need to frequently reposition the tracker, thus saving time and reducing the risk for errors.
For this application, we used the Scantech Trackscan-Sharp, a state of the art large scale 3D scanner. This unique handheld 3D scanning system system leverages state-of-the-art optical tracking technology and high-resolution cameras to deliver unparalleled accuracy and efficiency on large-scale parts and components.
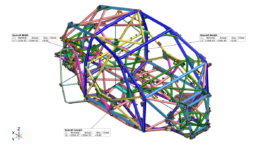