In the 2019-2020 financial year, no less than 449 million train journeys were recorded in the UK.
And although the pandemic reduced the number of passengers, trains remain the best and most-eco-friendly means of transportation. Here at T3DMC we work extensively within the railway industry with manufacturers, providing 3D scanning for product development and quality control for components and moulds.
Rail transport components are usually sizeable with many curved surfaces. Traditionally, measurement of very large railway components was time-consuming and not particularly accurate. Nowadays however, thanks to 3D scanning systems available on the market the problem of low-quality, low-efficiency can be easily overcome.
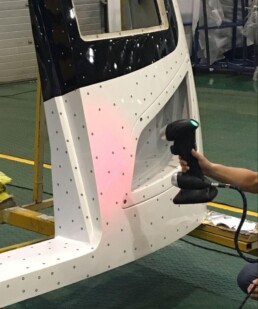
Detection of structural castings for train chassis
The structural casting for a train chassis is about 1200mm long, 600mm wide and 400mm high, and has a central platform supported by 6 cones. The casting has a medium-to-large size, multiple curved surfaces and angles. The diameters of different cross-sections of the six cones, the number of degrees of each angle, and the length and width of the central platform should be measured in order to provide data for subsequent processing.
To meet these needs of the engineering design process, we use the latest in 3D systems scan devices such as the KSCAN, which covers scanning area as large as 1440 mm x 860 mm per single shot and has a scanning speed of 1,350,000 measurements/second. These capabilities ensure the real-time scanning of medium to large sized components, reducing the duration of scanning and data processing to less than half an hour. This is an enormous benefit for reverse engineering and rapid prototyping project work.
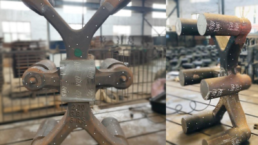
Locomotive manufacturing challenges
Mould making is one of the key procedures in metro train manufacturing. Metro locomotive manufacturing can be largely divided into the following procedures: design mould development manufacturing assembly. Metro train manufacturers need to perform 3D scanning over locomotive mould to achieve 3D measurement data, and then compared the data with original digital analog to calculate potential deviation values and thus increase product accuracy.
Due to the bulkiness of a locomotive mould, it is very difficult to ensure scan process accuracy when using ordinary 3D scanners. As a problem-solving company, we offer handheld 3D scanner systems with high resolution capabilities, as well as our unparalleled mechanical engineering expertise.
Our systems are ideal for high-precision measurement of geometric sizes for large-sized workpieces and manufacturing equipment, which can be coupled with Scantech 3D detection device in operation. Lightweight and easy to use, our scanners offer great portability whilst delivering a volumetric accuracy of 0.015mm/m. The system can easily cope with the measurement of ultra large-sized components and significantly increase measurement accuracy.
Compared with moulds, the 3D detection of metro locomotives poses more stringent requirements after they are manufactured. Questions like whether the overall error falls within the limit of design, whether the mounting holes of locomotive windows or doors are compliant with standards, are closely related to the safety and stable operations of metro trains.
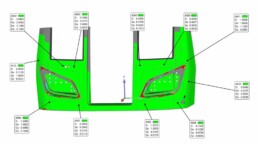