Scantech have demonstrated the endless benefits of 3D scanning in their recent project.
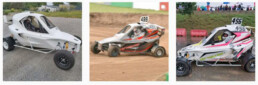
Using the KSCAN they helped France-based, LR Motor Company in developing a new product. Famous for its high-performance buggies, LR Motor Company’s chassis are strong, resistant to distortion and impact, and have a high bearing capacity. By scanning the tubular chassis of a race vehicle, they were able to create a CAD model which became the foundation for development of a brand-new model of racing car that can be used for competition.
The shape and structure of racing cars is much different to everyday vehicles, with a need for the car to have stability within a lightweight design. A tubular chassis is a complex shape, and because most of the chassis in this workshop are handmade, they are even more complex and unique. This means that traditional measurement methods that require contact with the measuring device would not have been appropriate for this project.
In addition, an effective way for inspection and maintenance is required for race cars. They are susceptible to wear and tear when used in competition and its essential that potential wear is identified on parts in time to complete vital maintenance. Once the competition season ends, manufacturers must also investigate how they can improve the performance of their vehicles – including the driving experience – which requires data of the previous components.
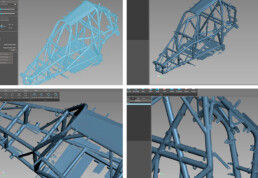