“I started designing the piece and then brought it to T3DMC for scanning… I had hoped to use the scan data to laser cut the box section, but the angles were too complex and nobody had a machine that was able to cut them. Neal had some ideas about how we could fabricate the piece together and jumped straight in.”
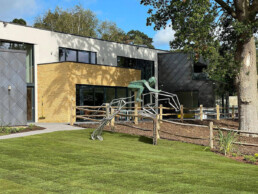
Jacob Chandler is an artist that needs no introduction here in the UK. His work focuses on dramatic points of action, be it physical or mental. Jacob’s sculptures have been exhibited in capital cities across the globe and have been highly commended by Royal societies.
Recently, Jacob received a challenging commission from a private client who wanted a statement piece comprising a horse and jockey to adorn their formal gardens.
The concept of the sculpture, incorporating bronze and steel, was going to be quite sizable at 3 metres tall and 3.5 metres long. Jacob was uncertain about how to manufacture it, so he quickly got in touch with the team at T3DMC with whom he had worked on previous sculptures to discuss the challenge.
The Design Process Reimagined
“As with all of my pieces I am trying to capture movement at its most dynamic point. If I can capture the horse’s form in its fullest, that will have the power that I am trying to create despite the lack of mass. The choice of materials has played an important role in this work – I imagined the horse would almost visually disappear and we’d have a floating form of the jockey. I started designing the piece and then brought the model to T3DMC for scanning,” says Jacob.
“I had hoped I could go from the scan to a box section laser cutter, but the angles were too complex and nobody had a machine that was able to cut them. Neal had some ideas about how we could fabricate the piece together and jumped straight in”.
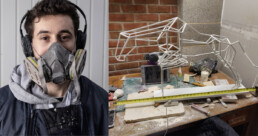
After discussing the requirements of the sculpture fabrication with Jacob, Neal Taylor, Technical Director at T3DMC, found a solution.
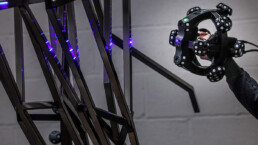
“Because each part of the horse was made from different stainless steel bars that had to come together seamlessly, we knew that we had to weld them at specific angles. We looked at the 3D design and we marked the angles on the steel bar, after which they were individually cut. We carefully put them in a framework with a grid reference created from the 3D data and then positioned them in the right place using clamps,” comments Neal.
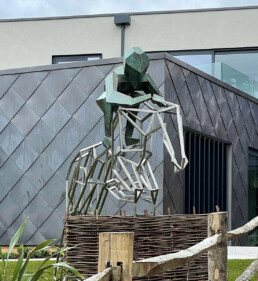
Project Support beyond 3D Scanning
The T3DMC team built as many parts inhouse as possible, employing two types of welding – MIG and TIG welding with stainless steel wires – to achieve the desired results. After fusing all the components together, the sculpture was cleaned down by filing the joints to create a smooth, flowing aspect.
“The welding itself wasn’t difficult, but the cleaning part was, as the jockey element is bronze and the horse is stainless steel,” adds Neal.
“Working with two different types of metal was challenging. What’s more, we had to assemble everything together so we came up with a three-pin solution for attaching the jockey to the horse. This in itself had to be almost invisible so that the jockey looks like he is floating above the horse – and I think we achieved that. Our idea was to have one pin on the underside of each foot and another one on the jockey’s chest and Jacob was very pleased with it!”
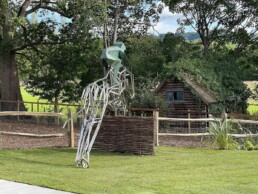
T3DMC’s team of engineers were able to assemble the jockey together with the horse and help move the project along to its final stages.
The sculpture, titled The Final Furlong, is now installed at the client’s property, where it stands majestically within its bucolic setting.
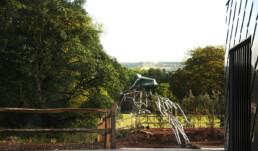
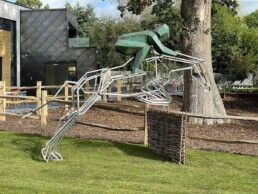