“The key factors that influenced our decision were quality of data and flexibility – which was enabled by the photogrammetry capabilities built into the handheld 3D scanner. They allow us to scan small and large objects alike.”
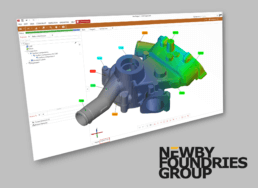
Midlands-based Newby Foundries Group produces and supplies high-quality lost-wax and sand castings in ferrous and non-ferrous materials. Recently, the company was looking for a solution that would improve its rapid prototyping workflow and also provide enhanced quality control and inspection reports for customers. Additionally, the new solution was also required to aid reverse engineering and product inspection to ensure conformity with the original CAD designs.
For years Newby Foundries had been using an external resource for their 3D scanning inspection and validation needs. The company manufactures automotive components, for which lead times are very short, alongside products found in the hydraulic, marine, petrochemical, and rail industries.
Investing in in-house 3D scanning
“When we got in touch with T3DMC we had some knowledge of 3D scanning, as we were using external scanning services for gathering our data and overlaying it onto 3D models”, said Raj Sidhu, Rapid Prototype Design Engineer at Newby Foundries.
“The issue we had was that the parts we need scanning on a daily basis range in shape and size from a few centimetres to a couple of meters long, so transporting them to and from the 3D scanning contractor to get CAD models was quite difficult at times. In addition, this process took time, which delayed our production schedules.”
The right tool for the job – The handheld AXE scanner
Realising that perhaps things could be simplified if they had their own 3D scanner, Raj contacted T3DMC, who offered a free onsite demonstration. After looking at different scanning systems available on the market, the AXE handheld scanner was chosen for its flexibility and reliability.
Portable, lightweight and cost-effective, the AXE laser scanner relies on powerful integrated photogrammetry software that delivers improved volumetric accuracy of 0.020 mm/m and absolute accuracy of 0.020 mm. These capabilities remove the need for additional devices or accessories. The AXE offers fast, accurate and detailed 3D surface data gathering of complex geometries. It effortlessly captures even the most tricky surfaces often found on fully machined components, making it perfectly suited to quality and design engineering projects from development to production.
“The key factors that influenced our decision were quality of data and flexibility – which was enabled by the photogrammetry capabilities built into the handheld 3D scanner. They allow us to scan small and large objects alike”, added Raj.
“But perhaps the greatest benefit we derived from using the AXE was that it enabled us to considerably shorten lead times through quicker and more reliable validation. If in the past we needed two weeks to turn around a typical component, now it only takes four days from concept to completion, thanks to the quick scan process. In addition to saving time, the system has also minimised our spend on external 3D scanning services – so much so that it has paid for itself in just one year!”
Detailed inspection powered by 3D scan photogrammetry
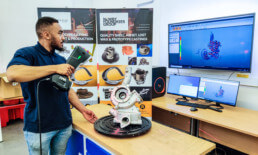
Further added value was provided by the creation of detailed inspection reports explaining variations and giving optimisation recommendations relating to specific scan objects and production processes. Quality control and inspection documentation are also created automatically, saving many hours of tedious manual work.
If like Newby Foundries you are looking at bringing in-house 3D scanning to your business and delivering quicker and more accurate components to your customers, simply get in touch. The T3DMC team will take the time to understand your processes and provide a solution that is guaranteed to save you time and money and optimise your route to market, delivering that competitive advantage!
Working closely with the customer
T3DMC has a responsive and skilled team of engineers who specialise in 3D engineering; specifically 3D measurement for design, reverse engineering and quality. We work with applications in every sector of industry from automotive and aerospace to consumer goods, casting, plastics and medical.
In addition, T3DMC is the UK exclusive distributor for market-leading 3D scanning equipment manufacturer ScanTech. This allows T3DMC to offer a range of portable 3D scanners that can capture complex surfaces quickly and accurately including chrome, aluminium and carbon fibre. The scanners are ideal for reverse engineering and quality applications of components where confidence in the data being captured is essential.
If you’re looking to bring your 3D scanning in-house, give us a call on 01746 762251 or drop us a note on info@t3dmc.com.
Other news articles